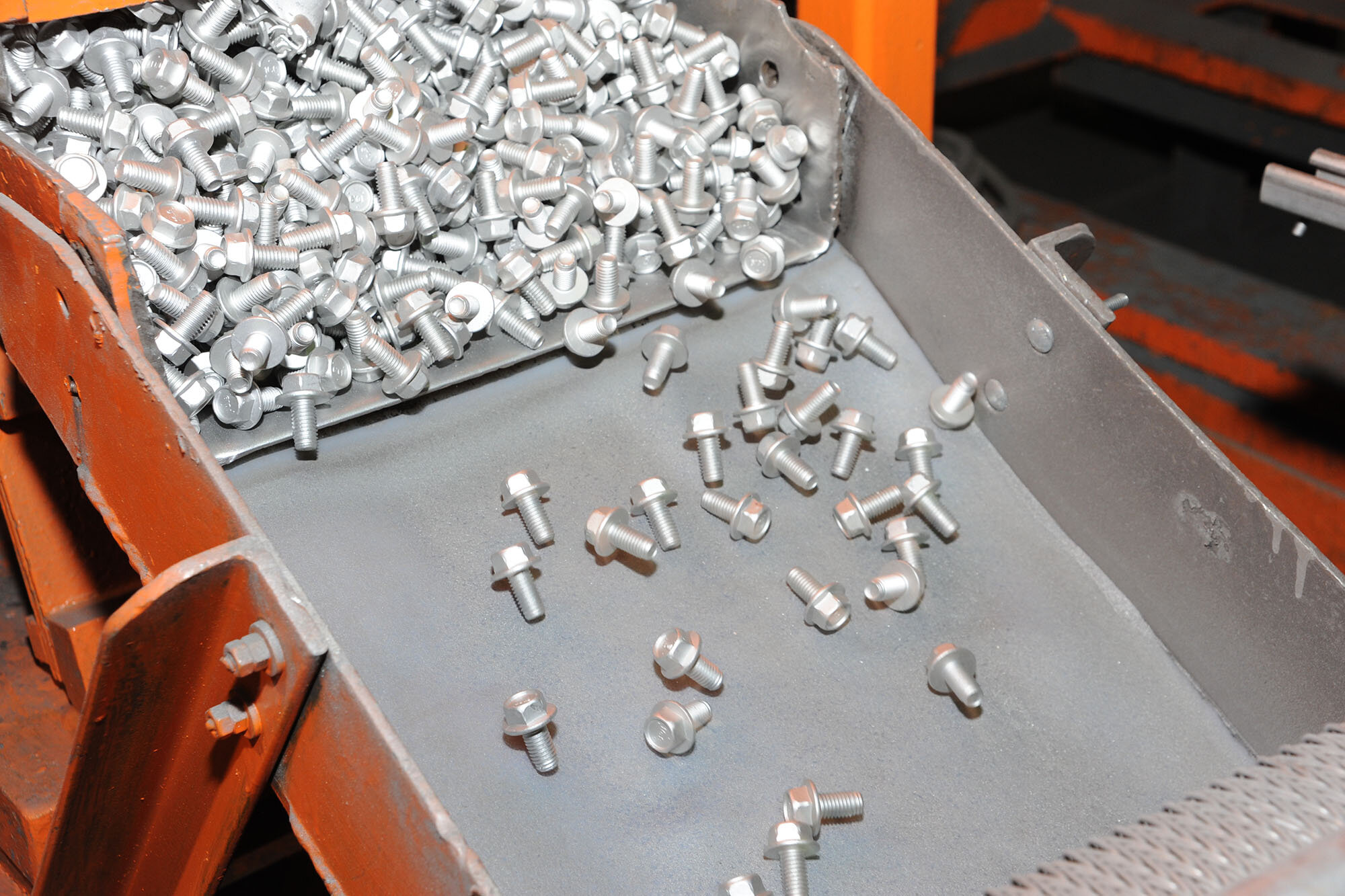
SERVICES
Dip Spin
Planetary Centrifuge Coater
Planetary motion takes its name from our solar system. Each of the planets revolves around the sun while simultaneously rotating about an individual axis.
The Benefits of Planetary Centrifuge Coating
This concept is now being utilized in state-of-the-art dip spin coating equipment to enable a coating applicator to coat very small and intricate parts without leaving too much coating on them.
Recess head screws, nuts, SEMS bolts, and KEPS nuts, washers, and stamped parts with bends, recesses, or areas that trap coating are difficult parts to dip spin coat in traditional centrifuge equipment without leaving an excess coating on the parts.
A planetary centrifuge coater eliminates this excess coating, creating the highest percentage of fully functioning parts of any dip spin coating equipment available.
Uniform Coating on Every Part
Similar to a traditional centrifuge coater, a planetary coater consists of a turnstile arm that holds the basket and creates the centrifugal force to revolve the basket.
Unlike traditional centrifuges, planetary coaters split the workload into multiple baskets to create the most uniform coating potential for every part. Parts to be coated are loaded into the baskets and the turnstile arm will position the baskets over a dip tank filled with coating.
The dip tank is lifted to submerge the parts in the coating and then is partially lowered from the baskets to allow the coating to drain and to allow the baskets to spin.
Cost Saving, High Quality
The excess coating is thrown off the parts by the centrifugal force of revolution during the spin cycle and collected by the walls of the dip tank saving paint loss.
The parts in the baskets will typically be spun at 200 - 250 RPM and then will be slowed down to a much slower revolution to enter the planetary cycle.
During the planetary cycle, the planetary centrifuge will continue to drive all of the baskets together in a single direction of revolution (such as clockwise).
At the same time, each of the baskets will individually be driven to rotate in the opposite direction of the revolutionary movement (such as counterclockwise). This rotation will change the position of each basket by 180 degrees.
A brake will stop the basket rotation quickly creating a centrifugal force of 30G to reorient the parts in the basket. Part orientation in the basket will be altered in several ways; first, a part facing toward the center of the basket will be redirected to face the outside of the basket.
Also, parts will change positions in the basket. This reorientation and movement will allow the coating trapped in recesses to flow out, alleviating excess coating on the parts.
Geomet
The GEOMET® topcoat system is a water-based coating containing metallic components such as zinc and aluminum flakes. The metal within the paint forms layers that create a great barrier for corrosion protection. Once the paint has cured at 600-610° F/320°C the coating becomes completely inorganic.
GEOMET® can be combined with a variety of topcoats to meet specific requirements related to torque tension, appearance, and salt spray.
Request for Quote
Chem-Plate Industries is ready to provide you with high-quality materials for your business. We provide a full spectrum of services and our highly experienced team can guide you in making the best decision. If you are interested in working with us click the link below to request a quote today!