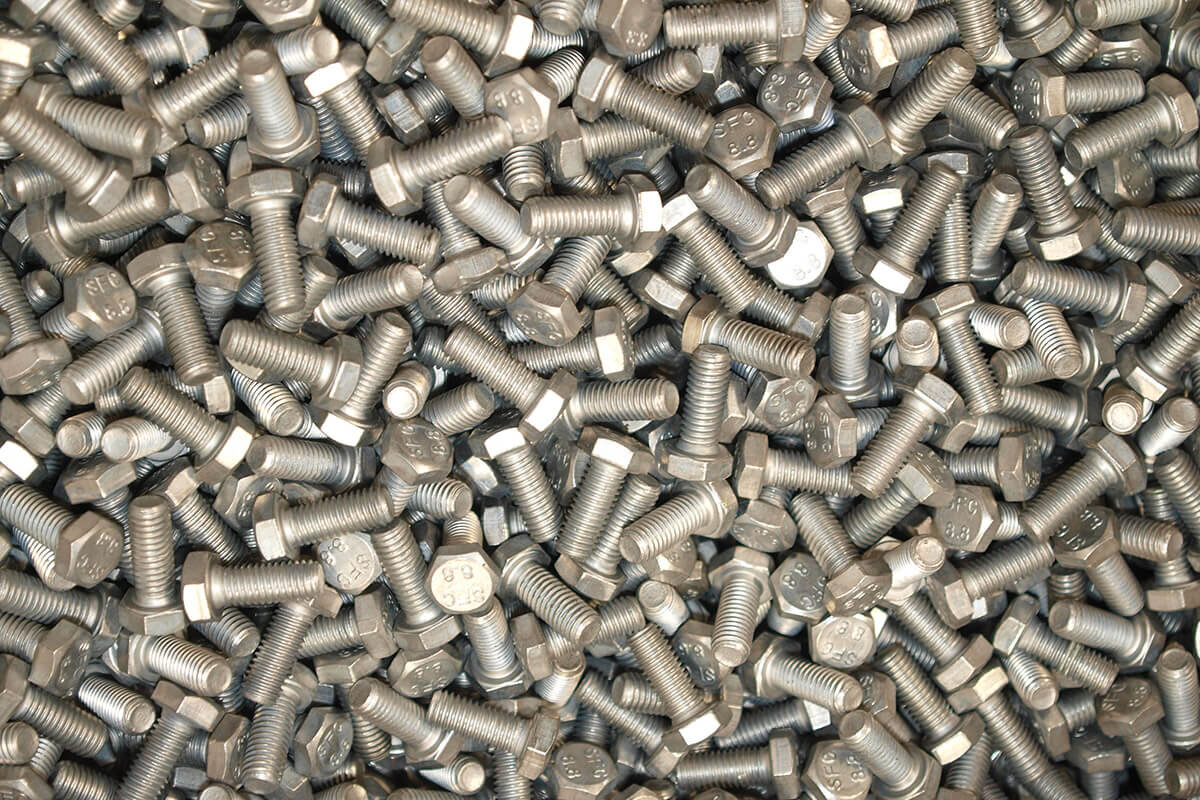
SERVICE
Plating
Chem Plate industries provide a range of plating services from Acid Zinc barrel plating to alkaline zinc-nickel barrel plating, phosphating, and mechanical plating to a large diverse set of industry standards, from construction to automotive.
We use industry-standard specifications followed by customizable top coating options to fulfill your finishing needs. For specific information regarding torque tension control, color, salt spray, and wearability, see our topcoat section or contact our sales team for more information.
Mechanical Plating and Galvanizing
Mechanical Plating is a type of metal finishing process that protects metal parts through the application of a sacrificial metallic coating onto the part. Parts are usually, but not limited to, steel or copper. This method of plating is also referred to as Peen Plating or cold welding.
Mechanical coatings can be applied on a much wider thickness range than electroplating and can also be combined with many different topcoats for a customized solution to meet a wide range of requirements. Mechanical plating topcoats can provide a range of colors, salt spray hours, torque tension tolerances, and many other specific industry needs.
Mechanical Plating, unlike Electro-Plating, does not utilize an electrical reaction or extreme temperature to coat the parts. Instead, it uses a combination of chemical reactions and kinetic forces of glass beads to cold weld the metal to the surface of the part. This process has many industry advantages, in both quality and cost. Mechanical plating does not produce Hydrogen Embrittlement and does not require a post-bake cycle*. Mechanical plating more easily coats odd-shaped parts from chains, to flat parts, to complex sintered metal parts, allowing a company to utilize one process for an array of applications and part types.
Additionally, compared to hot-dip galvanizing, mechanical plating does not require threads to be chased after plating.
At Chem-Plate Industries, we offer a wide range of mechanical plating processes including Standard Zinc Plating and Galvanizing, Silver Plating, Zinc Aluminum coatings, Tin Coatings, and our CP 2000 process which is a quad metal coating with salt spray in excess of 2,500 hours. Through the use of both propriety topcoats and partnerships with suppliers, we can offer mechanical plating with superior adhesion, salt spray, and appearance.
Chem-Plate Industries prides itself on providing a wide range of services to best fit all industries' metal finishing needs. We do not sell the customers just what we have; we have what the customers need. Having the ability to mechanically plate on top of our dip spin, electroplating, and ArmorGalv® processes gives us the unique advantage of being able to offer the best solution for whatever requirements you may have.
* If parts need to be stripped before Mechanical Plating, it is recommended that the parts be baked after the stripping process.
Non-Toxic Cadmium Replacement Coatings
We work closely with our sister company Straus Chemical Corporation to keep our processes ahead of the curve. Over the past few years, we have been working on new technology to replace and reduce the environmental impact problems associated with older toxic and environmentally harmful metal finishing technologies.
We have developed several Cadmium plating replacement options, each meeting the necessary qualities traditionally associated with Cadmium plating, specifically high corrosion resistance, lubricity, and anti-galling properties.
This is a mechanically applied Zinc/Tin alloy with high corrosion-resistant topcoats. It demonstrates all the attributes of Cadmium plating without its harmful health and environmental effects. Cad-Replace MZT7030 provides greater than 1,500 hours of NSS, and lubricity CoF 0.12-0.15, is REACH compliant, paintable, free of hydrogen-embrittlement, and available in various colors.
ArmorGalv® TT
ArmorGalv® TT is a Zinc/Iron thermal diffusion coating that replaces Cadmium for corrosion resistance on carbon steel (>2,000 hrs NSS) and to impart anti-galling properties (CoF 0.165) on any alloy of stainless steel. The coating is REACH compliant, non-toxic, highly abrasion-resistant, and free of hydrogen embrittlement.
Electro Zinc
Located at our Devon facility is one of the largest zinc plating lines in the area. Our specially-formulated Zinc plating system deposits bright, ductile, leveling, uniform (minimal dog-boning), lamilar, inherently higher-corrosion resistant Zinc than is readily available.
When combined with novel topcoats, corrosion resistance of 1,000 - 3,000 hrs of NSS is obtainable. Additionally, we have passivated available that are REACH and PROP65 compliant that is not easily commercially available for Zinc plating. Attached to this line is a continuous bake furnace, ensuring that your parts are in the oven and at 400°F within one hour after plating.
Zinc Phosphate
Chem-Plate offers fine grain, medium weight, and heavyweight Zinc Phosphate. Additionally, we offer wet and dry-to-the-touch oil topcoats to meet automotive NSS and Cof F requirements.
Alkaline Zinc Nickel
We use the groundbreaking environmentally friendly Coventya 3S Zinc/Nickel System (12-15% Ni). This is an extremely reliable process that provides for the direct plating on 410 Stainless Steel without the need for a “Flash Nickel Strike”, and also easily coats hard-to-plate Case Hardened parts.
This Zinc/Nickel plating system offers a bright, uniform finish, even in low current density areas, such as on clips and stampings. Very even distribution of the plating deposit allows for long parts to be plated uniformly, unlike most other electroplating processes. With a 12 to 15% Nickel deposit, this system offers exceptional corrosion protection when used with our trivalent passivates which are offered in clear or black. If a yellow finish is desired, our unique totally Chrome-free “NoKrom Y” passivity works great over the alkaline Zinc/Nickel base.
At our Morse facility, we added a state-of-the-art automatic plating line upgrade by Jessup Engineering. The process equipment is fully automated with a continuous bake facility directly in-line so that parts are automatically dumped from the plating barrel directly into an individual bin in the bake oven. This assures that parts reach 400F within one hour and avoid part mixing.
Request for Quote
Chem-Plate Industries is ready to provide you with high-quality materials for your business. We provide a full spectrum of services and our highly experienced team can guide you in making the best decision. If you are interested in working with us click the link below to request a quote today!